Group 5 DEL MUNDO

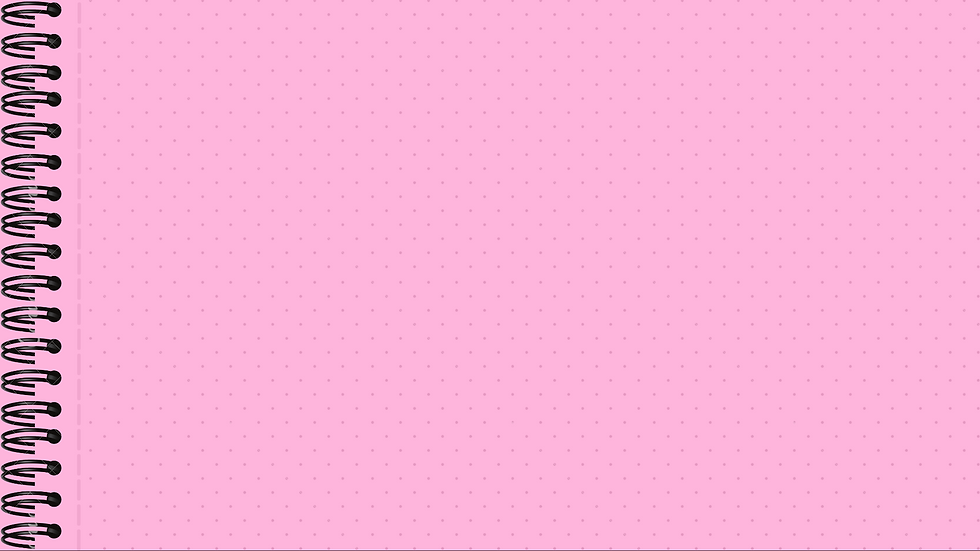

​
Research Design
The researchers employed a Completely Randomized Design (CRD) for their experiment. The simplest design for comparison studies is CRD, which solely makes use of the two fundamental elements of experimental design: replication and randomization. A CRD's experimental units or plots are completely randomly allocated treatments and can be used for trials with one or more factors (Frey, 2022). The researchers randomly grouped the carbonized CG samples and assigned a random treatment to the group, with three replicates each. In this experiment, the treatments were the varying CG-binder ratio: CG1(1:2.1), CG2(1:1.75), and CG3(1:1.87) and were compared to a control group of water hyacinth briquette made with cornstarch with 1:2.1 ratio. The stated ratios are based on a study by Carnaje et al. (2018) on WH briquettes and the guidance and recommendation of the research adviser from the Department of Science and Technology - Forest Products Research and Development Institute (DOST-FPRDI).
Methodology
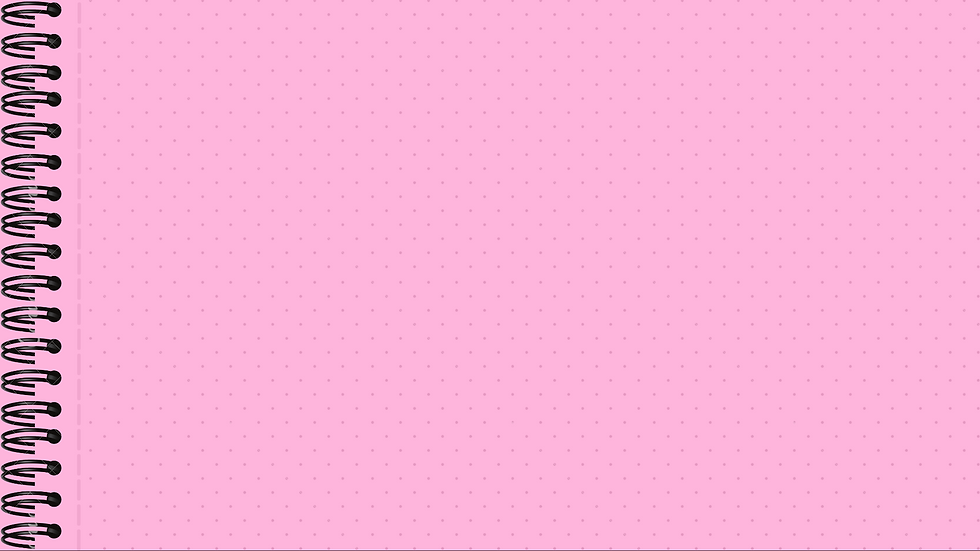


.png)
.png)
.png)
Plant Sample
Collection
Materials and Methods
A. Sample Preparation
Plant Sample Collection
The Cogon grass (Imperata cylindrica) of about ten (10) sacks was obtained from Gamu, Isabela due to its abundance in the area and the convenience of the location to the researchers. The water hyacinth (Eichhornia crassipes) of about five (5) sacks were collected from Pasig River with the help of the MMDA Hydraulic Control Structure in Makati.
​
Plant Sample Authentication and Preparation
The collected samples were then submitted to the Jose Vera Santos Memorial Herbarium of the Institute of Biology, College of Science, University of the Philippines - Diliman for identification and authentication of the species as Imperata cylindrica and Eichhornia crassipes. After this, the samples were washed thoroughly with distilled water, reduced into smaller pieces, and dried for two (2) weeks.
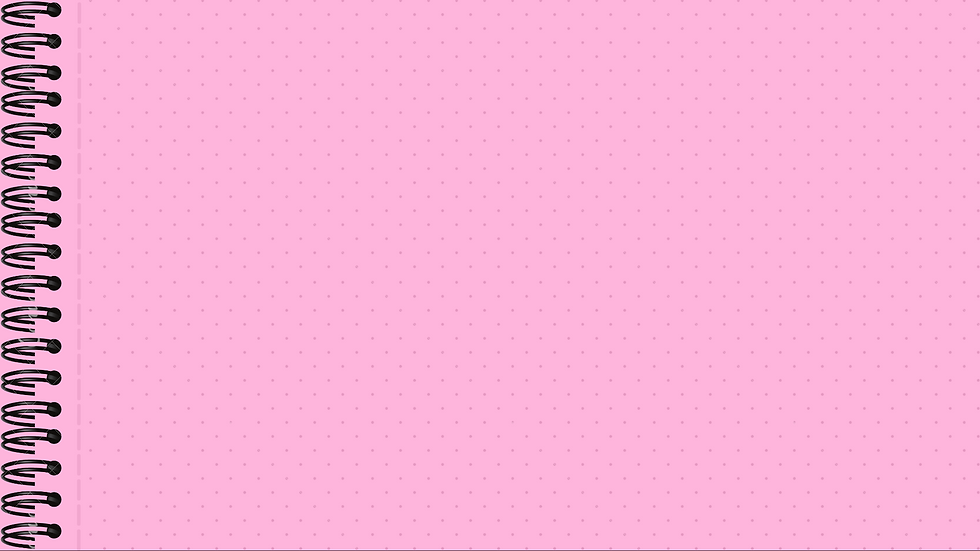

Carbonization
The samples were brought to DOST-Forest Products Research and Development Institute (FPRDI) for the carbonization process using the drum kiln method. A drum kiln is a modified 55-gallon drum with a length of 36 inches and diameter of 22.5 inches. It has a metal plate with a hole in the middle to cover the top opening of the drum kiln, a cylindrical chimney to direct the smoke out of the carbonizer, and three sets of air inlets to supply an adequate supply of air for combustion. To begin the carbonization, the chimney was placed upside down inside the drum kiln and the first layer of air inlets was opened. Next, the dried cogon grass was fed to the drum kiln at a manageable batch of 5kg or until the grass samples reach one-third of the carbonizer. Then, the chimney was pulled out to make a hole in the center of the raw materials, which served as a guide on where to put the fire. Once the ignition was sustained, the drum

could be fed with more grass samples until it was filled up. After this, the drum cover was placed back and the chimney was installed on top of the cover. When the lower level of the materials was already carbonized, the first layer of the air inlets was covered, and the second layer was opened. The same procedure was followed in carbonizing the middle layer and top layer of grass samples. The entire process usually takes an average of 6 to 8 hours and once it was over, the chimney was removed and the hole of the metal plate was covered. Also, the researchers made sure that all air inlets were closed so that no oxygen could get inside the drum kiln, which could cause the materials to become ash. The carbonizer was allowed to cool for 12 hours before discharging the grass sample and crushing them into powder form using a mechanized charcoal crusher. This machine is composed of a motor, a hopper to which the materials are fed, and a cyclone to collect the crushed materials. Before starting this process, it must be checked for any unwanted objects (e.g., rocks, metals, etc.) that may have been mixed with the carbonized grass to prevent the machine from being damaged. After this, its motor can be simply turned on and the carbonized cogon grass can be gradually poured into the hopper until all of them are turned into charcoal fines.
.png)
Carbonization
.png)
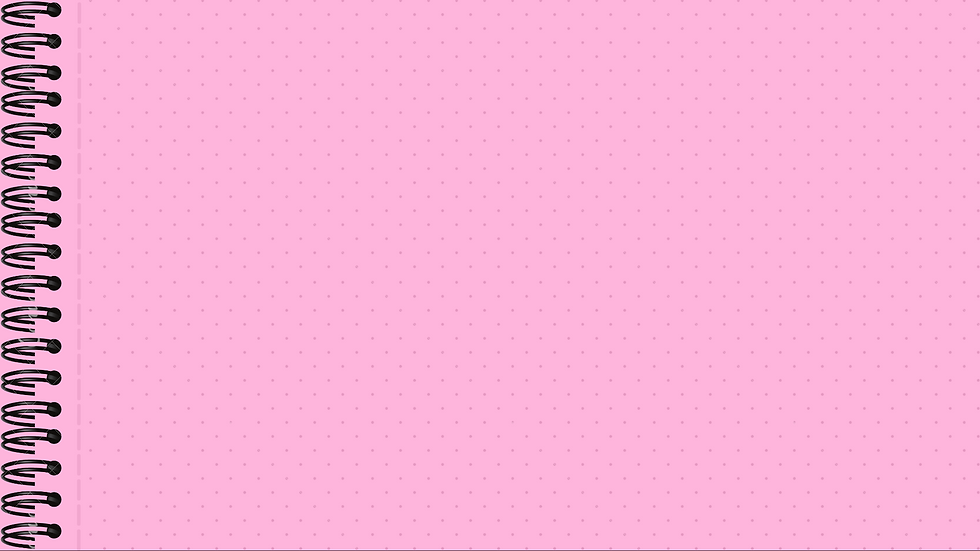
Mixing and Briquetting
Once the powder-like carbonized materials are collected, they were homogeneously mixed with cassava starch binder by hand. The binder was produced by dissolving cassava starch in boiling water. The amount of CS (in grams) and water (in milliliters) is 25-30% and 150-180% of the weight of the CG charcoal fines respectively. After achieving a dense mass from the combination of CG biochar and CS solution with a CG-binder ratio of CG1(1:2.1), CG2(1:1.75), and CG3(1:1.87), about 40g of the prepared mixture was pressed into cylinder-shaped briquettes using a manual charcoal briquettor. This equipment consists of a set of molds, cover plate, feeder, feeder drive, and lever. To utilize this for briquetting, the researchers began by placing the charcoal fines with binder into the feeder and pushing the feeder drive until it meets the set of molds so that the mixture could get inside. Next, the feeder drive was pulled to check if each mold was filled with the charcoal fines. If so, the feeder drive was pushed again and the cover plate was aligned with the set of molds. The lever was firmly stepped on to compress the mixture, then the feeder drive was pulled again before stepping on it once more to reveal the charcoal briquettes. Finally, they were transferred to a tray and sun-dried for 3 to 5 days. The combustible properties of this product were compared with water hyacinth briquettes made with a cornstarch binder as it has similar components with Cogon grass. The materials for the control group were chosen in accordance with the methods of Samahan ng May Kapansanan sa Taguig (SAMAKAT), a livelihood program producing WH briquettes for commercial use, and were made with a WH-binder ratio of 1:2.1 based on the recommendation of the research adviser from DOST-FPRDI.
From the three initial CG-binder ratios, the optimal concentration was chosen based on the data from proximate analysis, ignition time, burning rate, calorific value, and gas emission.


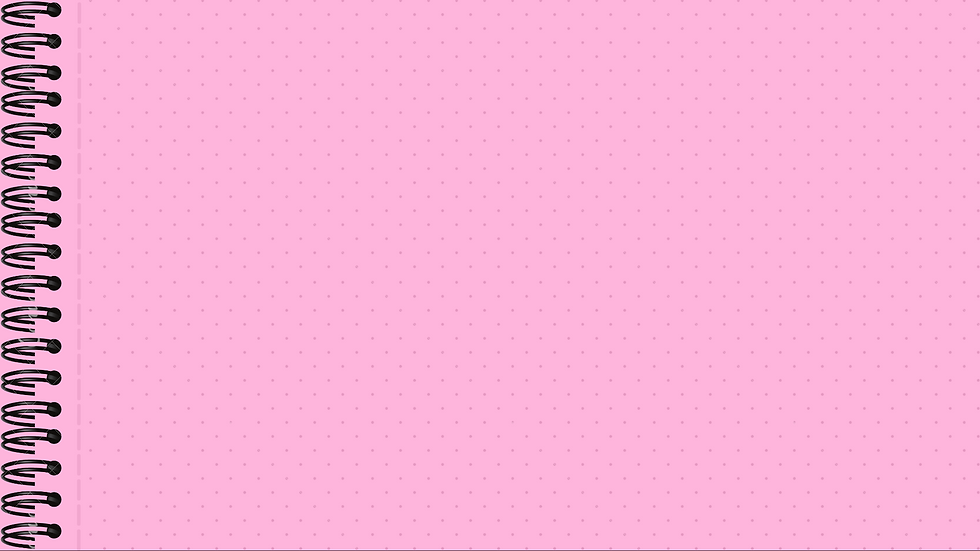

Data Gathering Procedure
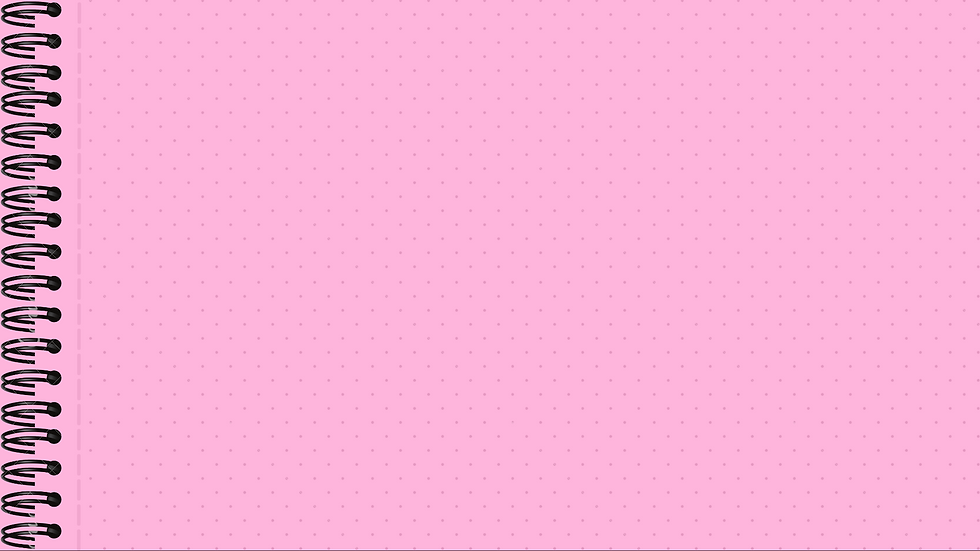

Proximate Analysis
Moisture, volatile matter, and ash content within the briquette samples were investigated through proximate analysis, following the standard methodology indicated in ISO 5068-1983, ISO 562:2010, ISO 1171:2010, respectively. This is aligned with the methods of the Department of Energy (DOE), where the tests were conducted. The nature of the sample and the testing method required it to be converted into a fine powder form. For the preparation process, it initially went through pulverization until it was able to pass through 60 mesh.
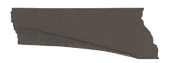.png)
.png)
Moisture Content. The process of calculating the residual moisture content of the CG briquette sample follows the two-stage method according to ISO 5068:1983. As the name suggests, this procedure consists of two drying stages which identifies the air-dry loss moisture and the residual moisture content. The sample was prepared by drying and grounding to a constant mass at 105 °C to 110 °C temperature with nitrogen. Air-dried samples must be able to pass through a 3,15 mm sieve to proceed. The weight of an empty weighing dish with the lid was recorded before the 10 g of the sample was placed into it. The dish's final weight after the sample was added was then noted.
A nitrogen-flushed oven that was preheated to between 105 and 110 °C is filled with the sample-containing dish at a rate of roughly 15 oven-volume changes per hour. Afterward, the dish was removed, cooled for 10 mins on a thick metal plate, and transferred to a cooling vessel until it is at room temperature.
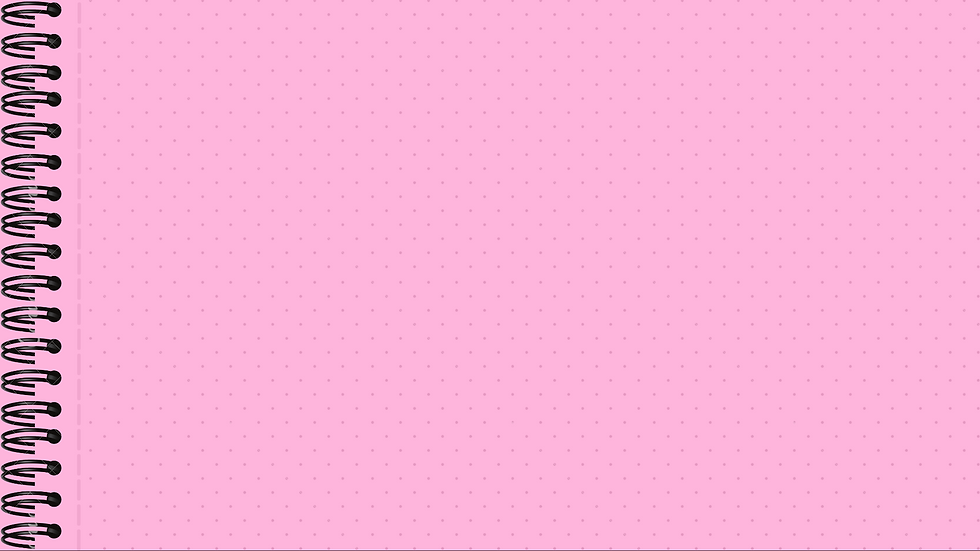

Volatile Matter. The methodology outlined in ISO 562:2010 was followed to determine the volatile matter content. It was assessed using a general analytical test sample of charcoal that has been ground to the point of passing through a 212 μm aperture sieve. The sieve is a fine mesh strainer used to control the distribution of the particle size of the sample as it needs to be well-blended and have the same amount of moisture as the lab environment. For the furnace temperature checking, the zone in the furnace, which contains either a stand with one crucible and a
lid or a stand with the necessary number of crucibles and lids, should be heated at approximately 900°C as shown by thethermocouple. It
should be verified that the temperature under each crucible is within the uniform zone's temperature tolerance at the same height. For the volatile matter determination, a stand was inserted into the oven, either with one empty crucible with lid or with the necessary number of empty crucibles with lids. It was kept at approximately 900°C for 7 minutes. The crucibles were then taken out of the furnace and laid out on a heavy metal plate to cool to room temperature. Once cooled, the empty crucibles and lids were weighed, with roughly 1 g of test sample placed into each crucible, to the nearest 0.1 mg. The cover was then replaced, and each crucible was tapped on a sterile, firm surface until a consistent layer of test material formed on the bottom of each one. The furnace's door was closed for 7 minutes while the charged crucibles were placed in a cool stand and relocated. The crucibles were taken out and cooled until room temperature. The empty crucibles were then weighed to the closest 0.1 mg while they cooled to limit the impact of any water film that had been adsorbed on their surface. Additionally, quick cooling lessens the amount of moisture that the charcoal residue will absorb.
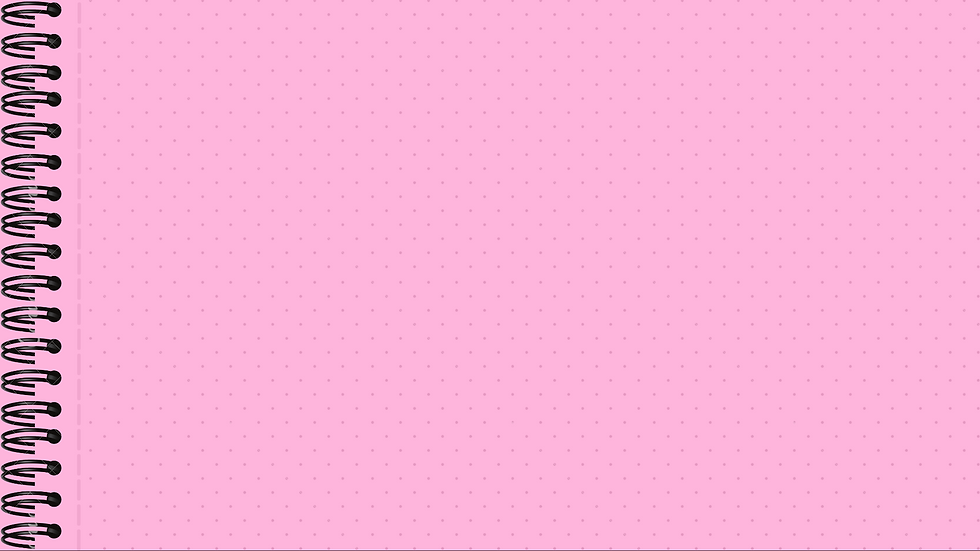


.png)
.png)
Ash Content
Ash Content. The ash content was calculated in accordance with the method specified in ISO 1171:2010. The coal used for the general analytical test sample was powdered so that it may pass through a 212 μm aperture sieve. The sample was thoroughly mixed and had moisture levels that were in balance with the lab environment. The dish was weighed to the nearest 0.1 mg, equally distributed 1 g of the sample throughout the dish, and weighed again. The sample was spread roughly 1 g uniformly in the dish, weighed again to the nearest 0.1 mg, cleaned, and dried. Before determining the initial mass of a silica or porcelain dish, it was heated to 805 °C to 825 °C, held there for 15 minutes, and then cooled in accordance with the guidelines for the actual determination. At room temperature, the dish was placed in the furnace. For a total of 60 minutes, the furnace's temperature was gradually raised to 500 °C, then maintained for 30 minutes. A 60-minute holding period at 500 °C is required for brown coals. The dish may either be placed in a second furnace that has previously been preheated to 805 °C to 825 °C or heated for 60 minutes in the same furnace at 805 °C to 825 °C. After the dish had been incinerated, it was removed from the furnace and allowed to cool for ten minutes on a heavy metal plate. When the cooling period was through, the dish was moved to a desiccator or another closed container sans desiccant, and cooled down to room temperature. The
weight was measured to the closest 0.1 mg after cooling. To prevent the accumulation of moisture during cooling, the container was flushed with dry gas. Reheated at 805 °C to 825 °C for additional 15-minute intervals if there is any uncertainty that the incineration is incomplete (for instance, if unburned carbon particles are visible). It is repeated until the mass change does not exceed 1 mg.

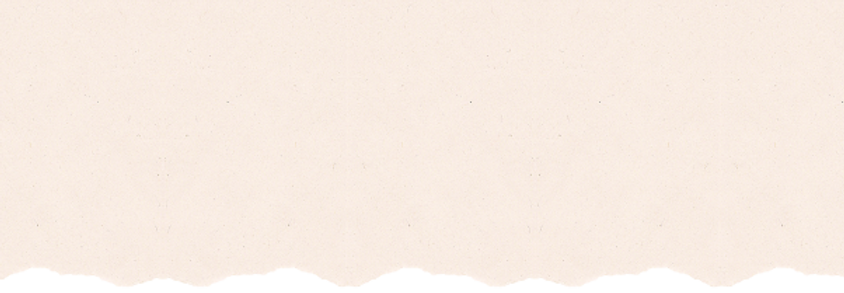
Calorific Value
Measuring the calorific value of the Cogon grass briquette followed the standard test methods issued under ASTM D 5865-13, also following the methods of the DOE, where it was performed. It is used to determine the gross calorific value of coal through an isoperibol or adiabatic bomb calorimeter. This instrument is used to measure the amount of heat emitted from the sample combustion.
The calorimeter bomb and vessel were initially assembled and prepared together with a sample of benzoic acid to identify the heat capacity of the calorimeter to be used. A weight of 0.8 to 1.2 g of benzoic acid was placed into the instrument's sample holder. An amount of 1.0 mL of water was added to the bomb, then the sample holder was placed inside. Afterward, it was filled with oxygen through a constant pressure between 2 and 3 MPa. The assembled calorimeter bomb was placed in the calorimeter vessel that was filled with room-temperature water. Each test run must have a fixed amount of the materials and must ensure that the oxygen is controlled to prevent the benzoic acid in the sample holder from blowing up. Once it was set up, the sample was fired and the temperature rise and stabilization is observed, which was used to calibrate the heating capacity of the calorimeter.
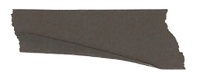.png)
.png)
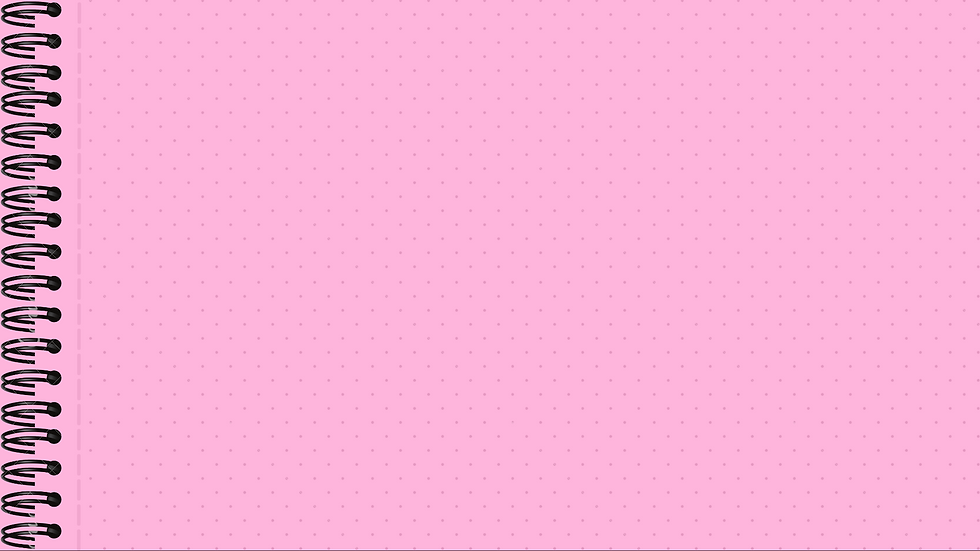

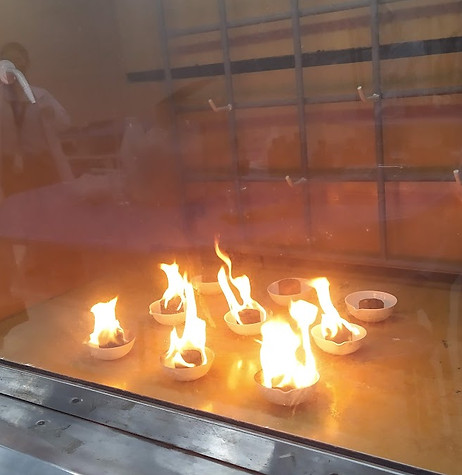
.png)
.png)
.png)
IT
Ignition Time and Burning Rate
The ignition test and burning rate of the briquettes were determined by the researchers using the Makati Science High School laboratory. Nine samples of dried briquettes were prepared for each ratio of CG and WH, with each one assigned to an evaporating dish and labeled accordingly. Before conducting the tests, the weights of the evaporating dishes, the individual briquettes, and the sample on the dish were recorded. The briquettes were then mixed with one of the three different amounts of kerosene: 0 ml, 5 ml, and 10 ml, with triplicates of each amount, per ratio. Then, they were placed inside the fume hood for combustion. Based on the first visible indicator of ignition until the last, the ignition time was computed. Along with this, the mass burned per unit of time is used to calculate the burning rate. The samples were lighted one at a time and the time it took to burn a specific amount of briquettes was documented. The mass of the charcoal burned is the difference in weight between the original and final weights of the charcoal.
&
BR
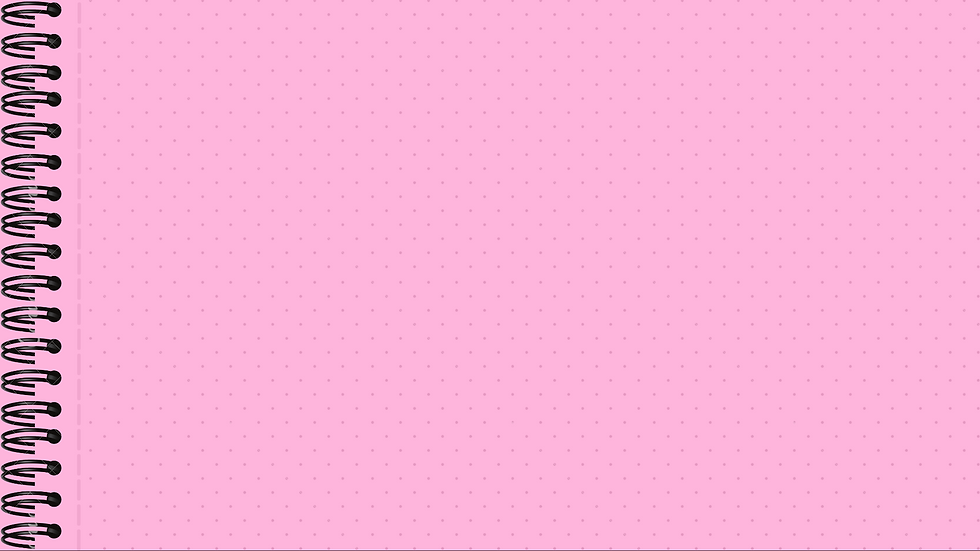

Gas Emission Analysis
The Gas Emission Analysis used a Flue Gas Analyzer to measure the amount of gas emission from the combustion of CG briquette samples and WH briquette control group. The following gases were analyzed: Nitrogen oxides (NOx), Carbon dioxide (CO2), Carbon monoxide (CO), and Oxygen (O2).
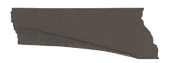.png)
.png)

Data Analysis
Multivariate Analysis of Variance (MANOVA) was used in this study to evaluate the significant group differences, between the CG briquettes with different CG-binder ratios and the control group of WH briquettes, across the multiple characteristics. This analysis takes into account the correlation established between the briquette characteristics, mainly proximate analysis, calorific value, ignition time, and burning rate. MANOVA assesses whether this relationship significantly affects the results of each variable in the different setups. If the p-value is less than 0.05, then the researchers will reject the null hypothesis. However, if the p-value is greater than 0.05, the researchers will fail to reject the null hypothesis.
In addition, as gas emissions did not have a significant relationship with the other briquette parameters, a One-way Analysis of Variance (ANOVA) was also employed in the study. This statistical analysis was used to identify significant differences between the values from the gas emission analysis of the CG briquettes with different CG-binder ratios as well as the control group of WH briquettes.
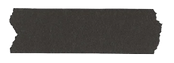.png)
.png)
.png)
.png)